Industrial environments demand improved and efficient material handling, making cranes indispensable to heavy-duty operations, especially due to their unparalleled lifting capabilities. Cranes can also effectively handle loads weighing hundreds of tons. However, since these machines are massive, there are associated risks of potential hazards such as collisions, electrical accidents, trip-overs, and failures.
Reports suggest that every year in the United States, 44 people meet with fatal crane accidents on average. Crane collisions, in particular, can lead to devastating consequences. This is where advanced sensing systems can help minimize the possibility of such incidents.
Sensors can detect potential mishaps and enable real-time control, which is crucial to crane collision avoidance systems. Let’s understand the sensor types typically used for crane collision avoidance and how to pick the right one for your specific application.
Types of Sensors Used in Crane Collision Avoidance
The current dynamic industrial environments involve human-machine collaboration, requiring enhanced safety measures. This is why crane systems are optimized using effective anti-collision solutions designed with a combination of sensors for greater precision and performance.
Browse our different sensors used for crane collision avoidance
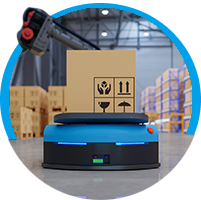
LiDAR (Light Detection and Ranging) Sensors
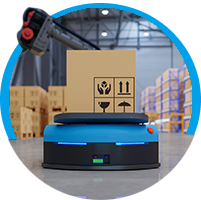
These sensors are capable of real-time mapping and, thus, provide 360-degree coverage of the crane’s surrounding area. LiDAR sensors can scan the operational area, identify potential collisions, trigger alerts, and take necessary actions. They are also highly accurate in data collection and 3D modeling.
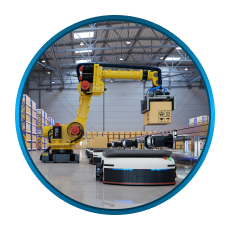
Safety Laser Scanners
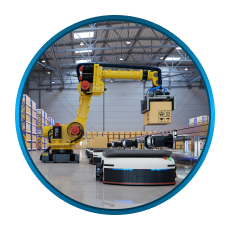
Safety laser scanners are widely used for high-risk machinery and automated industrial operations, as they can create a protective field to stop hazards. These can be configured for different needs and seamlessly integrate with existing systems to detect intrusions and prevent hazardous scenarios. Safety laser sensors also help define customized zones and boundaries for multi-dimensional crane travel patterns.
Optical Lasers
These sensing solutions provide precise, non-contact measurements with the help of focused laser beams. They have high-resolution detection capabilities with fast response time and can cover large working ranges. This lowers the chances of accidents and enhances industrial safety. Therefore, optical lasers largely cater to the crane collision avoidance requirements.
Key Features to Look for in Collision Avoidance Sensors
Leveraging advanced sensor and control technologies is essential for optimal performance and improved safety. Here are the key features to look for in crane collision avoidance systems.
Detection Range and Coverage
Cranes often operate in large, open, or semi-open spaces such as warehouses, shipyards, and construction sites. Therefore, it is crucial that the sensor reliably detects objects (both horizontally and vertically) at distances sufficient to stop or slow down the crane movement.
For instance, Hokuyo’s RSC-30 LN has a wide scanning angle and detection range, along with area-setting software that can be configured into any programming application.
Reliability
Precision and accuracy are of utmost importance regarding collision avoidance systems. Although cranes operate at slower speeds, even minor collisions can lead to severe consequences. Therefore, the sensors must offer high positional accuracy to determine precise distances to other objects and respond effectively.
Sensors used for crane systems must also possess high resolution for better accuracy, which is useful, especially in cases where cranes operate in tight spaces or near sensitive equipment.
Durability and Resistance
Since crane operations involve indoor and outdoor environments, collision avoidance sensors must withstand temperature fluctuations, noise and vibrations, electric and mechanical stresses, and extreme weather conditions.
Durable and resistant sensors with IP (Ingress Protection) ratings of IP65 or higher can perform reliably over a long period. Protective coatings and shields can be used for better protection.
Easy Integration
Collision avoidance sensors must also seamlessly integrate with the crane control logic to avoid significant infrastructural changes and minimize operational disruptions and implementation downtime. Sensors with standard communication protocols such as CAN, Ethernet/IP, Modbus, etc., are easy to integrate.
Hokuyo’s KAD-300 allows easy installation and maintenance with limited hardware. It can also be configured into various frequency drives and stepped controls.
Advanced Sensing Solutions
Implementing advanced sensing solutions offers substantial benefits like improved performance efficiency, productivity, and profitability. The right sensors can add immense value and reduce risks, delays, and errors.
For instance, Hokuyo’s crane collision avoidance sensors, like KAD-300 and RSC-30LN, can integrate with the existing working environment. They have flexible object detection capabilities and can reduce collision between overhead cranes, monorail systems, and fixed objects or obstructions within the crane operational area.
Are you looking for smart sensors to avoid crane collisions?
Explore our range of crane collision avoidance sensors or contact us for unparalleled service and support.