Warehouses worldwide are adopting autonomous technologies to improve efficiency, reduce errors, and lower operational costs. The global warehouse automation market, valued at $19.23 billion in 2023, is expected to experience a compound annual growth of 16.7% from 2024 to 2030.
Key industry insights, as per the BlueBotics survey, also showcase the rise of automation in warehousing:
- Over 70% of companies have adopted or plan to adopt AGVs or autonomous mobile robots (AMRs), and 21% already use self-driving forklifts in warehouses.
- Numerous organizations use AGVs to address staff shortages instead of reducing workforce size. This primarily includes material handling and packaging tasks.
- 91% of respondents in the survey plan to expand their AGV or AMR fleets.
- One-third of the businesses cite on-site safety as a major reason for choosing automation.
Hokuyo has engineered a special range of laser distance sensors to support this strategic shift in the warehousing industry. These LiDAR distance sensors are crucial in helping warehouses achieve higher autonomous capabilities while remaining safe.
Current Challenges in Automated Warehouses
Integrating autonomous capabilities is in your business’s best interest, but it can face numerous challenges without the right equipment.
Limited Space & Efficient Storage Usage
The preponderance of modern warehouses operate in compact layouts to maximize storage capacity. However, to achieve this, they’ve to face the tighter spaces, especially with towering racks and narrow aisles. This further creates challenges for automated guided vehicles (AGVs), forklifts, and robotic arms.
However, if a laser distance sensor is used, it can provide real-time measurement of rack heights and available storage space. Therefore, the placement of goods and navigation of automated vehicles will become precise and collision-free.
For example, a robotic forklift equipped with a laser distance sensor can safely deposit and retrieve pallets without damaging goods and warehouse infrastructure. Some automated stacking cranes (ASCs) can also use laser sensors to monitor pile heights, which reduces the risk of it crumbling apart and risking a human life.
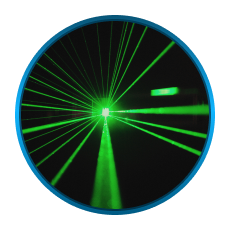
Laser Distance Sensors Prevent Collisions
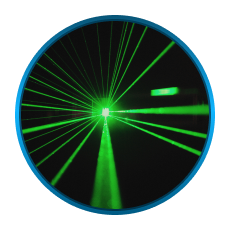
The AGVs, robotic arms, and fast conveyors are increasing the normal movement speed of goods in a warehouse. Cobots are also widely deployed in warehouses, working alongside humans to help expedite operations.
However, this human-robot collaboration poses great risks of collisions between robots or human workers. Such incidents can lead to costly downtime, equipment damage, and, most worrisome, fatal injuries or human loss.
Laser distance sensors can reduce such risks by sending signals to the robot to slow down or stop its function if a foreign object penetrates its programmed periphery.
Path Optimization & Goods Loading
Besides the tighter aisles, the paths of a robot or AGV can be blocked because of objects lying on the route. Without laser distance sensors, the chances of AGVs crashing and damaging goods are higher.
However, when the sensor is mounted, it can stop and signal human supervisors to clear the path.
Similarly, laser distance sensors can instantly scan package dimensions, position, and shape in automated sorting centers. Therefore, your warehouse can have an optimized sorting sequence, reducing the misplacement of goods.
During the loading and unloading of goods in trucks, the laser beams can detect empty spaces and guide the robotic arms or human crane operators to use the space optimally.
Inventory Management
Earlier, most warehouses relied on barcode scanning and manual stock checks, both of which were prone to errors. However, in automated warehouses, an outdated inventory system can cause overstocking, misplaced goods, and shipment delays.
Laser distance sensors are a perfect solution for optimizing inventory management by feeding real-time capacity data to warehouse management systems. The sensors can continuously track inventory and detect the distance (quantity) of goods programmed to be within a certain limit.
When that limit is reached, the supervisors will know there’s no space to place more goods in a specific location.
Use Hokuyo Laser Distance Sensors to Optimize Automated Warehouse Operations
At Hokuyo, we build the industry-leading PGL series laser distance sensors for indoor and outdoor industrial measurement applications. These automated LiDAR sensors provide high millimeter accuracy over long distances, making them suitable for warehouses.
These laser sensors can measure distance on natural surfaces, liquids, and even reflectors, providing you with complete versatility to program them according to warehouse environments.
Features | PGL-050W3 | PGL-180W3 |
---|---|---|
Measurement Range | 0.05~50m (natural surface) | 0.05~180m (natural surface) |
Accuracy | ±3.0 mm | ±3.0 mm |
Measurement Speed | Up to 100 Hz output rate | Up to 100 Hz output rate |
Serial Interfaces | RS-232, RS-422/485, SSI, and USB | RS-232, RS-422/485, SSI, and USB |
Dimensions | 140x78x48 mm | 140x78x48 mm |
Weight | 350 g | 350 g |
Material | Main Sensor Body: Aluminum Alloy EN-AW 6060 (Anodized 20um) Sensor front & Standard exchangeable cover: Mineral-reinforced nylon resin 7 |
Main Sensor Body: Aluminum Alloy EN-AW 6060 (Anodized 20um) Sensor front & Standard exchangeable cover: Mineral-reinforced nylon resin 7 |
Protection | IP65 | IP65 |
Operating Temperature | -40°C to +60°C | -40°C to +60°C |
Upgrade your automated warehouse with accurate and durable laser distance sensors to achieve next-level efficiency and safety. These sensors act as the eyes of AGVs and warehouse robots.
At Hokuyo, we research and develop advanced sensor solutions for all kinds of industries. We believe in accurate, efficient, reliable, and safe industrial automation, so we engineer sensors that meet these modern expectations.
Contact us to learn which laser distance sensor will be suitable for your organization.